Decided to start this thread to keep a record of what I found. Now keep in mind that I have NO electrical or mechanical background whatsoever, so if ANYTHING is incorrect, please let me know!
After a lot of reading, I finally came across this write-up that explained things very well compared to everything else:
http://www.stinsonclub.org/PublicTech/Y ... theory.pdf
I personally found it to be very informative and cleared up a lot of things for me when it came time to putting things back together and repolarizing my generator.
So to start, here is what my generator looked like prior to everything, I labeled the terminals just to be clear what goes where:
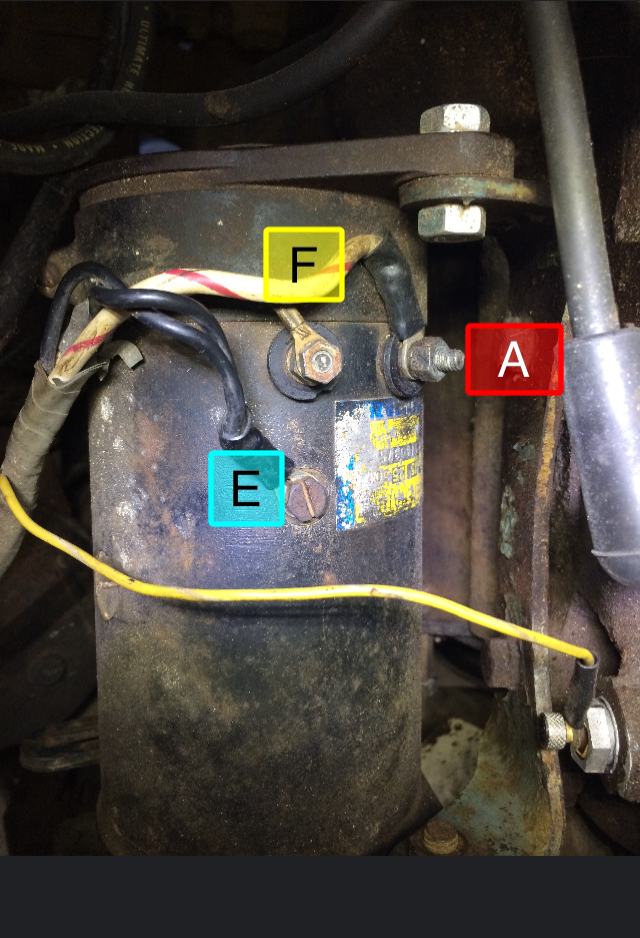
DO NOT throw anything away! Something I thankfully found out right away. The generator is pretty much ALL metric. In addition to this, ALL the terminals and the two long bolts holding everything together are M5 x 0.9 thread pitch. This is difficult to nearly impossible to find. So unless you'd like to drill and tap new threads, I suggest keeping everything in a safe place.